主減速器在汽車的傳動(dòng)系統(tǒng)中起到降低轉(zhuǎn)速,增大轉(zhuǎn)矩,同時(shí)改變轉(zhuǎn)矩旋轉(zhuǎn)方向的作用,其由一對(duì)或幾對(duì)減速齒輪副構(gòu)成,依靠齒數(shù)少的齒輪帶動(dòng)齒數(shù)多的齒輪實(shí)現(xiàn)減速,采用圓錐齒輪傳動(dòng)改變轉(zhuǎn)矩旋轉(zhuǎn)方向,主動(dòng)錐齒輪即是此部分系統(tǒng)中重要的傳動(dòng)組成部件,其將動(dòng)力輸入,并傳遞給從動(dòng)齒輪,實(shí)現(xiàn)控制汽車轉(zhuǎn)向系統(tǒng),調(diào)整內(nèi)外車輪線速度,從而實(shí)現(xiàn)汽車車輪平穩(wěn)轉(zhuǎn)彎。
錐齒輪的加工工藝為:下料→熱鍛造→正火(預(yù)先熱處理)→粗加工→精加工→滲碳淬火→回火→精磨成型。預(yù)先熱處理可以消除奧氏體組織的不均勻分布,消除鍛造過程中產(chǎn)生的應(yīng)力,減少裂紋出現(xiàn)的機(jī)會(huì),改善切削加工性能,為最終的淬火、回火熱處理做準(zhǔn)備 。
本文研究的汽車主減速器齒輪未到正常服役期時(shí),發(fā)生異常斷裂,該件設(shè)計(jì)標(biāo)準(zhǔn)要求表面有效硬化層深 0.8 ~ 1.1 mm,表面硬度 58 ~ 64HRC,基體硬度 32 ~ 48HRC。對(duì)此,進(jìn)行了全面分析檢測(cè),為后期生產(chǎn)提供一定的理論指導(dǎo)。
一、分析檢測(cè)
宏觀觀察
主動(dòng)錐齒輪輪齒大部分?jǐn)嗔?,未斷裂輪齒根部也已出現(xiàn)宏觀裂紋,觀察斷裂面,可在其中兩處斷齒上發(fā)現(xiàn)有明顯貝紋線裂紋擴(kuò)展痕跡,屬低周疲勞斷裂,圖 1 為主動(dòng)錐齒輪實(shí)物圖。
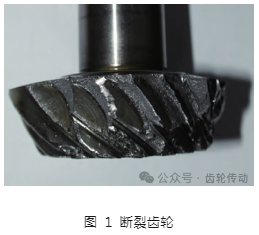
化學(xué)成分
采用直讀光譜儀測(cè)定輪齒表層化學(xué)成分,齒輪材質(zhì)為 20CrMnTiH 鋼,化學(xué)元素分析結(jié)果如表 1 所示,符合 GB / T 3077—2015 《合金結(jié)構(gòu)鋼標(biāo)準(zhǔn)》中各元素含量的要求。
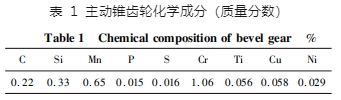
硬度試驗(yàn)
在殘留齒面及基體內(nèi)部取樣,分別測(cè)定各部分洛氏硬度,試驗(yàn)結(jié)果如表 2 所示,基體檢測(cè)值接近設(shè)計(jì)要求下限。齒輪表面平均硬度值低于設(shè)計(jì)要求,且硬度不均,表面硬度差距數(shù)值梯度大,說明表層存在異常組織,組織的不均勻性造成了硬度的差異。
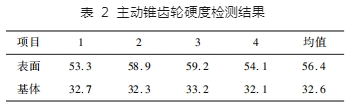
表面有效滲碳硬化層深度測(cè)定
在表層 3 點(diǎn)處位置取樣,利用顯微維氏硬度計(jì)測(cè)量獲取齒輪表面有效硬化層深度平均值,為 0.86 mm (要求 0.8 ~ 1.1 mm),硬度界限值 550HV1。依據(jù)標(biāo)準(zhǔn)(GB / T 9450—2005《鋼件滲碳淬火硬化層深度的測(cè)定和校核》)鋼件滲碳淬火硬化層深度的測(cè)定和考核,測(cè)量結(jié)果超過要求最低值,符合設(shè)計(jì)要求。
金相分析
在斷齒處制取金相試樣,經(jīng)粗磨、精磨、拋光,在金相顯微鏡下觀察非金屬夾雜物(其會(huì)破壞基體組織的連續(xù)性,改變材料力的分布形式,并在此處產(chǎn)生應(yīng)力集中),在斷裂附近及基體均未發(fā)現(xiàn)明顯非金屬夾雜物,只存在少量球狀氧化物,均在 1 級(jí)以下,如圖 2 所示。因此其不是齒輪斷裂的主要原因。
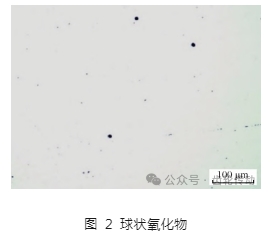
將拋光好的試樣經(jīng) 4% 硝酸酒精浸蝕,洗凈、吹干、顯微觀察,未斷裂的齒輪表面滲碳硬化層顯微組織為細(xì)針馬氏體 + 少量殘余奧氏體,如圖3 所示,其顯微組織屬正常淬火后產(chǎn)物;心部顯微組織為板條狀貝氏體 + 索氏體(圖 4),該組織會(huì)導(dǎo)致齒輪抗彎強(qiáng)度降低。但鑒于位于心部位置,不是主要受力部位,對(duì)齒輪斷裂影響不大。
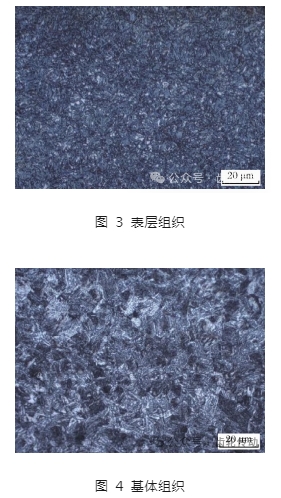
斷裂的齒輪根部表面存在網(wǎng)狀非馬氏體組織,測(cè)試其深度約為 0.04 mm(圖 5)。滲碳(碳氮共滲)在淬火后零件表面理想的組織應(yīng)該為細(xì)針狀高碳馬氏體,但因?yàn)闊崽幚砉に嚰凹庸すに嚨裙ば蛑T多不可控的因素,在齒輪表面形成了貝氏體、屈氏體(珠光體類)等一些非馬氏體的混合組織,造成了嚴(yán)重的質(zhì)量缺陷。非馬氏體組織深度如果超標(biāo)嚴(yán)重,在力學(xué)性能上就會(huì)出現(xiàn)零件表面硬度低的現(xiàn)象,影響硬度梯度,出現(xiàn)測(cè)試硬度不均勻的結(jié)果。
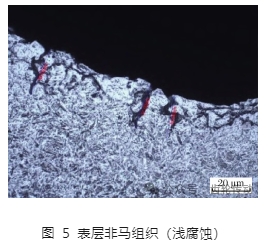
齒輪齒根部存在非馬氏體組織,國(guó)家汽車行業(yè)標(biāo)準(zhǔn) QC / T 262—1999《汽車滲碳齒輪金相檢驗(yàn)》規(guī)定齒輪表面非馬氏體組織最深不得超過 0.02 mm,該齒輪表面非馬氏體深度為 0.04 mm,且呈網(wǎng)狀沿原奧氏體晶界滲透。較深的非馬氏體組織嚴(yán)重降低了齒輪表面硬度和耐磨性,以及疲勞極限,并由晶粒邊界或氧化物的應(yīng)力集中區(qū)域萌生細(xì)微裂紋,形成裂紋源,使齒輪在后期服役嚙合時(shí)因抗彎強(qiáng)度不足而斷裂。
二、檢測(cè)結(jié)果討論
該齒輪表面有較深的非馬氏體組織,且呈網(wǎng)狀沿原奧氏體晶界滲透,該組織嚴(yán)重削弱齒輪表面及晶界強(qiáng)度,降低耐磨性和齒輪疲勞壽命(在相同作用力下,裂紋源的早期萌生,或者累計(jì)的裂紋損傷程度大都會(huì)降低齒輪疲勞系數(shù),從而降低疲勞極限壽命),非馬氏體組織的存在首先造成齒輪表面硬度不均,使齒輪在服役過程中,易產(chǎn)生應(yīng)力集中,而出現(xiàn)疲勞裂紋源,多裂紋源的繼續(xù)擴(kuò)展最終導(dǎo)致齒輪斷裂,使齒輪的疲勞壽命大大縮短,這是齒輪失效斷裂的主要原因。
三、改進(jìn)措施及效果
解決非馬氏體組織產(chǎn)生的源頭有兩個(gè)主要途徑:一是選材時(shí)盡量減少會(huì)優(yōu)先選擇性氧化的元素(不同元素被優(yōu)先氧化的順序?yàn)?C > Ce > Ba > Mg > Al > Ti > Si > B >V >Nb > Mn > Cr> Cd > Fe > P > Mo > Sn > Ni > As > Cu);二是減少滲碳?xì)夥盏难趸越M分(如降低氧分壓等),解決目前國(guó)內(nèi)齒輪問題,選擇第二種方式更易被生產(chǎn)商接受。
具體措施為:(1) 非馬氏體組織的產(chǎn)生說明熱處理爐內(nèi)有氧化氣氛,應(yīng)提升爐內(nèi)滲碳?xì)夥盏臐崈舳?,?yán)格控制熱處理爐的密封性,可適當(dāng)延長(zhǎng)熱處理爐的排氣時(shí)間,使?fàn)t內(nèi)的滲碳?xì)夥崭儍簟?2) 本次失效的齒輪表層整體硬度偏低,適當(dāng)提高表層硬度,可以提高齒面接觸疲勞強(qiáng)度。保證滲碳前工件表面的清潔度,提高表層硬度及均勻度。(3)滲碳過程中由于齒根部碳勢(shì)較高,且冷卻速度較其他部位慢,故齒根部易生成非馬氏體組織,需適當(dāng)增加齒輪的淬火冷卻速度,以達(dá)到減輕或消除此缺陷的目的。
四、結(jié)語(yǔ)
依據(jù)改進(jìn)建議,進(jìn)行了熱處理工藝調(diào)整(包括氧化氣氛及淬火冷卻工藝),對(duì)新一批的齒輪進(jìn)行了抽樣取點(diǎn)觀察,未發(fā)現(xiàn)明顯的網(wǎng)狀表層非馬氏體組織。徹底消除此組織對(duì)材質(zhì)及熱處理工藝要求均很高,工藝的調(diào)整大大改善了齒輪表層的組織缺陷,從最終分析結(jié)果及改進(jìn)后的效果可以得知,本文分析方法的有效性較高,且能為齒輪的處理工藝提供一定的指導(dǎo)意義。